How The Fabricator Has Evolved To Meet The Needs Of The Architectural Community
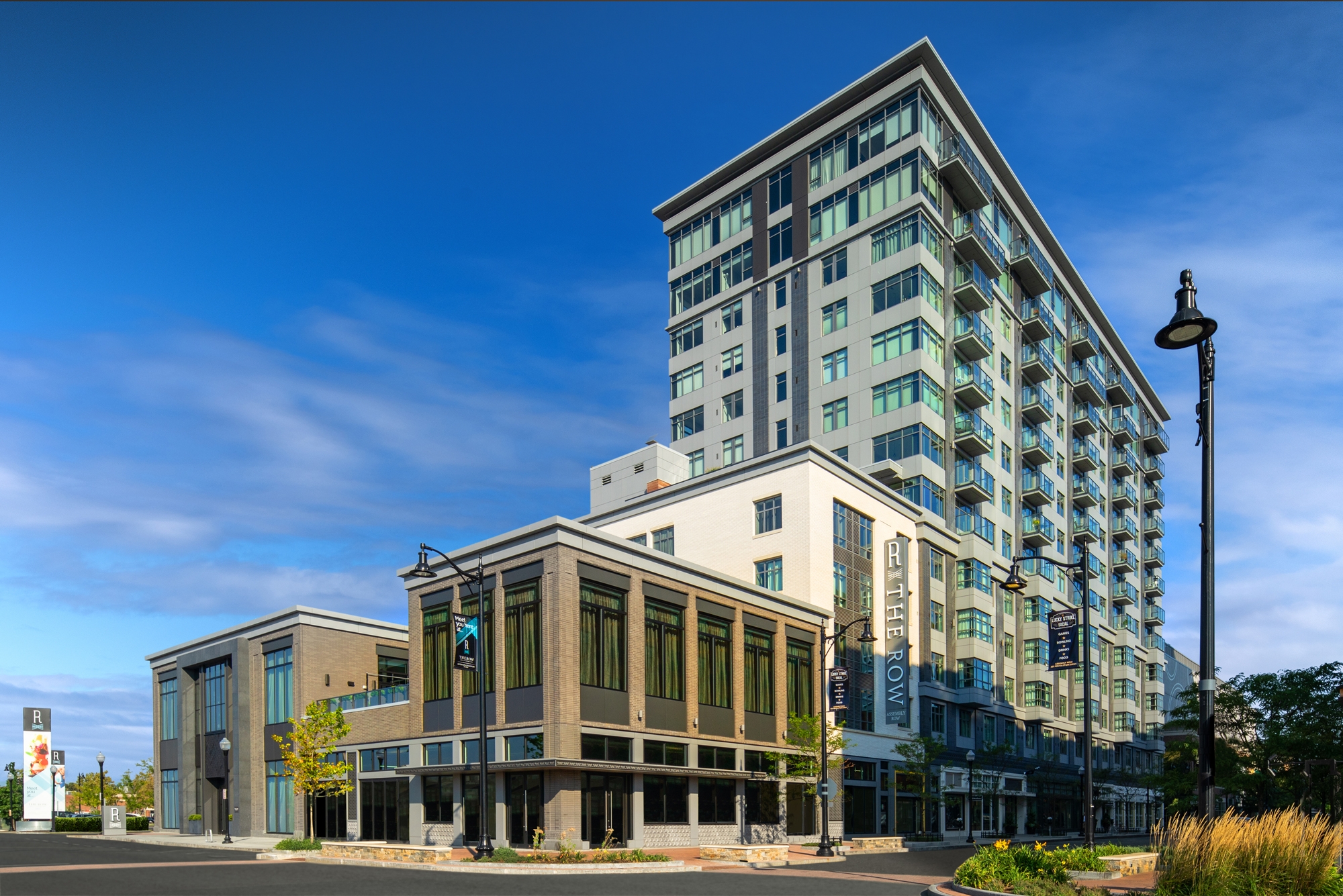
Over the last two decades, fabrication has dramatically changed. Traditional cladding materials such as glass, stone and metal now share the architectural space with cladding products such as fiber cement and high-pressure laminates. The evolution of materials has influenced the growth of the fabricator. As architects seek shared wall space exteriors, it is the fabricator’s responsibility to stay abreast to new trends and adapt to architecture’s ever-changing trajectory.
In the past, the fabricator was largely seen as an executor whose only responsibility was to provide an attachment system along with the fabricated prechosen material. Technological advancements were often seen only in the production process with the fabricator having limited involvement in the design process as a whole. And, of course, the main drivers of a given project were not the fabricators but in fact the material manufacturers.
Today, the fabricator is seen as a solution-driven partner who helps and assists the architect in the design process. Fabricators no longer possess a product bias having a wide array of materials from different and competitive manufacturers. Fabricators were once single-material specialists, and some remain that way today. Yet, the modern fabricator has shifted to carrying numerous products as a response to the architectural movement towards less monochromatic and more diverse façade design.
The selection process for materials is two-fold including surface or system selection, each with different features and benefits. The modern fabricator can advise the architect on how selected products can be attached to a building exterior. In addition to visual capabilities, materials and systems are selected based upon code compliance, cost efficiencies, availability, sustainability, and the total wall assembly. The total wall assembly is a particularly important component when multiple surfaces are specified.
Additionally, a fabricator’s technological understanding of the total wall assembly is far more expansive. Modern fabricators have specialty training and staff to stay abreast to the latest building codes, trends and software. This is important for an architect seeking a design assistant who has compatible software and the ability to create customized panel and high performance rainscreen systems.
These sophisticated system technologies help determine the precise panel dimensions, virtually eliminating human error on a building exterior. The modern fabrication team can seamlessly integrate 3D laser scans with BIM Models for the prompt execution and submission of as built drawings for production.
Fabricators also now possess in-house engineering capabilities and have an extensive knowledge of code compliance and adherence. Equally as important as software capabilities, is the ability for a fabricator’s team to have on-site personnel who can create models and determine the best solutions for an architect seeking a compliant or sustainable solution.
Unlike a manufacturer whose product is tested, a fabricator is responsible for the testing of the total wall assembly. As such, it is paramount that cladding systems meet and/or exceed all of the project specific requirements for performance adherence to local & International Building Code standards. Depending on the system chosen, a fabricator should clearly identify what tests and procedures were completed internally and with third party assistance.
Unlike the fabricator of the past, today the modern fabricator is seen as a solution-driven partner to the architect.