High Rise Debuts in Downtown Maryland With Iconic Metal Façade
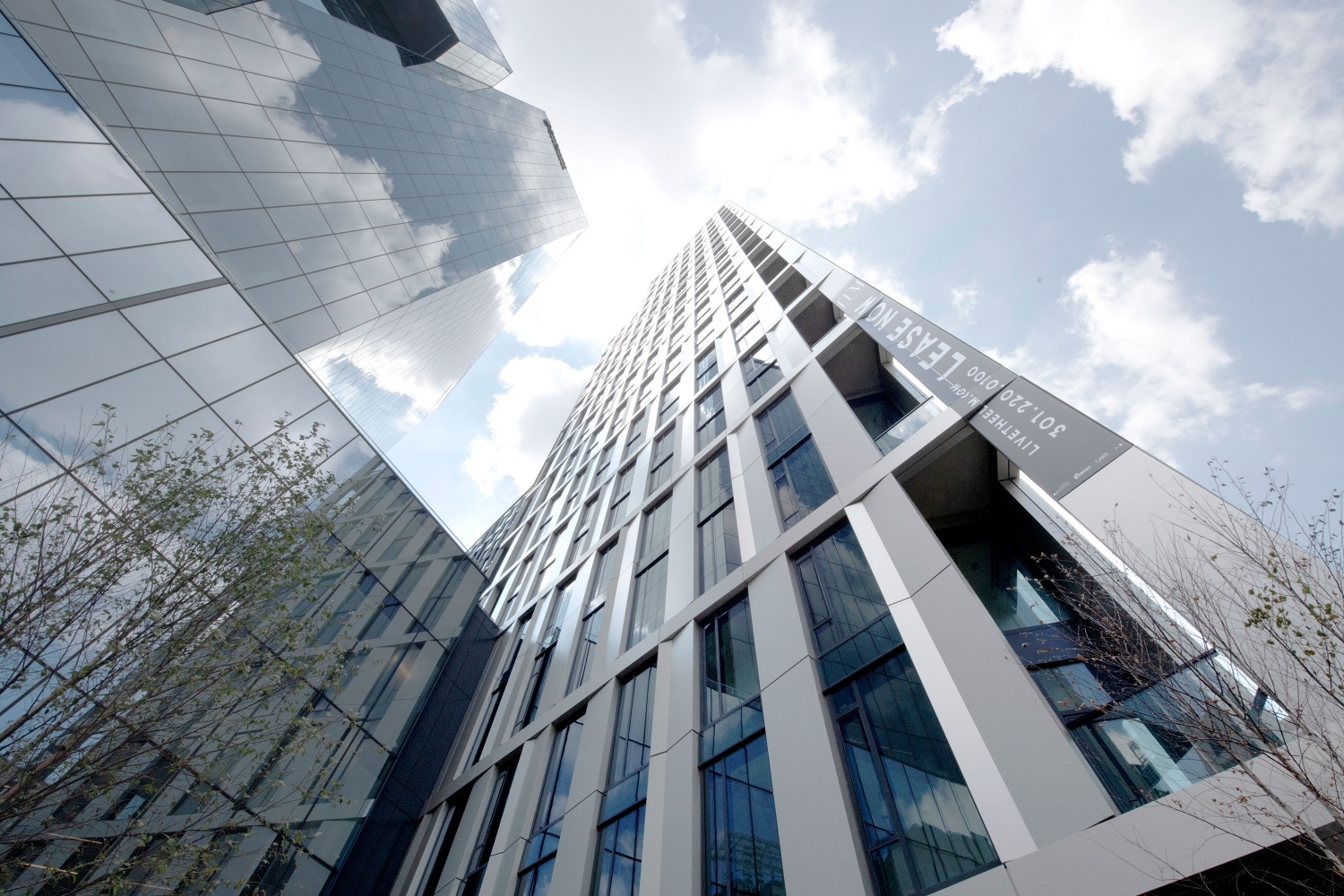
Project Name: | 7272 Wisconsin Ave/The Elm |
Location: | Bethesda, Maryland |
Architect: | Shalom & Baranes Associates (SBA) |
General Contractor: | Clark Construction |
Products: | 4mm ALUCOBOND® PLUS in Anodic Satin, NaturAL Brushed Carbon, and two custom colors |
CEI Materials System: | R4000 and a custom engineered rear drained back ventilated direct-attached system |
Photography: | CEI Materials |
Rising thirty stories high in downtown Bethesda, Maryland is a new iconic structure called the Elm, a 1,000,000 square foot mixed-use property. “The Elm is the tallest building in Bethesda and an extremely complex project that has taken over five years to complete,” explains Steven Lee, Senior Façade Technical Designer at Shalom & Baranes Associates (SBA) in DC. The neutral tones of the residential high-rise are juxtaposed by the glass curtain wall of the office façade.
The tower’s base is constructed with dark brick, with ALUCOBOND® PLUS aluminum composite panels covering the remaining portions of the colossal façade. Given its height, the design team was required to develop unique engineering criteria to meet inherent wind load and movement requirements. CEI Materials, a part of the design team, worked closely with SBA to engineer a panel cladding system that accommodated these complex design needs.
According to Nick Sodt, General Manager at CEI Materials and Project Manager of the Elm, “We constantly worked with the architect on such things as joint layout and panel stretch and designed integrated spline joints to help with the ease of installation at extreme heights with building movement.”
Four ALUCOBOND® PLUS aluminum composite finishes were chosen, Anodic Satin, NaturAL Brushed Carbon, and two custom colors. Nearly 200,000 square feet of material was fabricated by CEI Materials utilizing both the R4000 system as well as a custom engineered rear drained back ventilated direct-attached system.
Visually, the building is extremely tall with numerous geometric angles that required large panels and a grid system to create a flat, solid look. Working together with SBA, CEI Materials built an onsite performance mockup to test the structural integrity of panel size and connections. This test would determine if the proposed design would address water and specific project requirements for building movement and deflection. The mockup was tested off-site by Intertek at their facility and not only passed but also gave the team a clear visual indication of what the façade would look like in reality.
A chevron design was created as an adaptation for the building’s geometric design. According to Lee, the chevron panel design also affected the building’s energy efficiency and NFPA 285 adherence. Typically, a 2" cavity has to be filled with insulation for the LEED Gold requirement, but the chevron design afforded a 6" hollow cavity when it came to this project. Therefore, it was decided to increase the depth of the insulation, thus leaving no gaps that would have likely led to a possible chimney effect, as seen in high-rise building fires around the world.
When installing such a large project, fabrication material scheduling and onsite delivery were vital. Therefore, careful consideration had to be given to panel fabrication and its adaptation for installation. CEI Materials possess the in-house technology to track the progress of each fabricated piece and its delivery to the job site. This process enables the installer, and the rest of the design team, to calibrate the material delivery timing and therefore maximize labor costs.
The Elm, and its neighboring façade, the Wilson, were recently awarded the Engineering News-Record (ENR) Mid-Atlantic Regional Best Projects Award in the Best Office/Retail/Mixed-Use Project category.