CEI Helps Architects Complete Stunning Adaptive Reuse Project In Watertown, Massachusetts
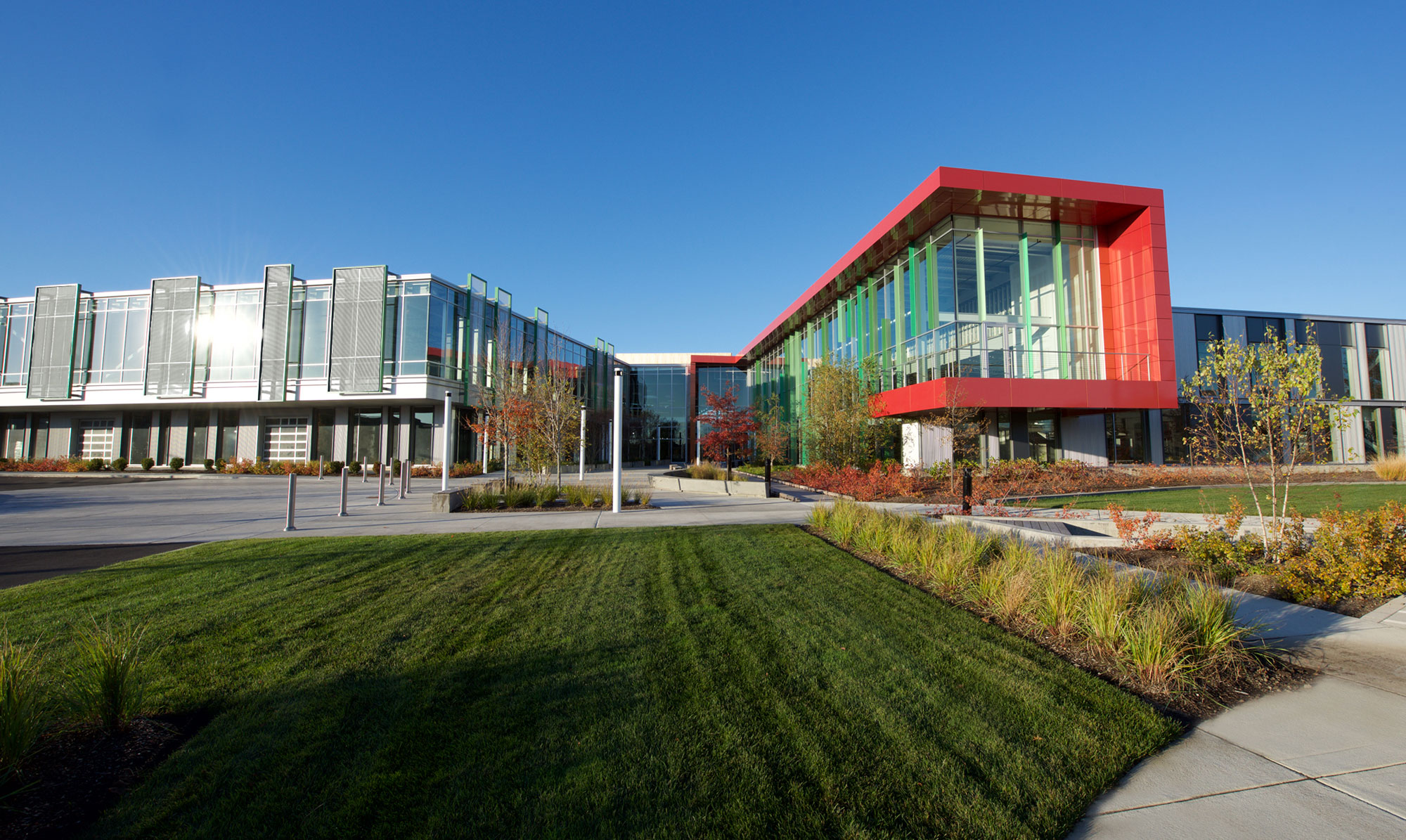
Project Name: | The Linx |
Location: | Watertown, MA |
Architect: | Spagnolo, Gisness & Associates |
General Contractor: | Callahan, Inc. |
Installer: | TR Construction |
CEI Materials System: | R4000 |
Products: | MCM, Single Skin, Modular |
LEED: | LEED-Certified |
Photography: | CEI Materials |
The Linx is a $60 million adaptive reuse architectural marvel by Spagnolo, Gisness & Associates (SGA Arch) in Watertown, MA. The building was converted from a concrete warehouse into a contemporary commercial office complex with a design that incorporates daylighting and various exterior-cladding materials. With the concrete replaced with glass, the new building was split into two and will now house a variety of professional industries from technology to health insurance.
The 185,000 square foot structure was developed by Boston’s Boylston Properties and sits in East Watertown, an underdeveloped area. While areas like Kendall Square are prime real estate and considered the “gold standard for Boston-area companies seeking office space,” describes the Boston Globe, developers like Boylston Properties are seeking out underused, underdeveloped areas to invest in to cultivate new commercial interest just out of reach of the Boston/Cambridge area.
John Sullivan, of SGA, explains the industrial redesign of the Linx, describing the façade as having “depth” due to the wide range of materials it utilizes and the purposefulness of the building’s “light-filled atrium lobby with a café and lounge.”
Garrett Harris, Project Manager at CEI Materials describes, “The Linx was a chance for CEI to showcase our expertise in large-scale projects. Our team fabricated over 50,000 square feet of metal material. We had an opportunity to fabricate two different manufacturer’s MCMs and also Morin’s perforated and corrugated panels. Additionally, we got to showcase our growing interest in modular construction.”
The MCM from manufacturers Reynobond and Alucobond, utilized both companies’ fire-retardant core materials. The metal composite material featured in finishes Pewter, Anodic Clear and Alucobond’s Spectra Cupral.
The various single-skinned components were Morin’s C-29 corrugated panel and Morin C-40 perforated panels, which were used on the sunshading screen walls integrated into the exterior design. Additionally, the prefabricated/modular structures used Alro’s ¼” wall aluminum tubing.
Jason Sherrill, COO of CEI Materials explains, “There are numerous benefits to modular construction including shortened lead times, reduced intrusion to existing businesses, less trades to coordinate with the GC and reduced cost. For the Linx, it additionally removed room for human error and also reduced on-site waste. We utilize the modular process often in the automotive market, but it’s becoming more prevalent in the various architectural markets like commercial construction as well.”
With the multitude of metal components used on the project, CEI overcame a variety of challenges related to the design, fabrication and installation. Harris further explains, “We had a C-Shaped panel that ran between the first and second floor that was sandwiched between window heads and window sills. Taking all the variations around the entire building and designing a common panel that would align and fit correctly was a challenge.”
Additionally, vertical fins were designed that ran from the second floor and to the first floor angled sill, designing their correct angle as it varied around the building required much accuracy.
Lastly, Harris states, “We worked closely with the general contractors at Callahan Inc. and the installers at TR Construction. We were able to overcome any challenges and the resulting building really speaks for itself.”